The spot welding machine is used for the purpose of welding by simultaneously energizing the electrode butt weldment and utilizing the Joule heat (instantaneous) generated by the contact resistance between the electrodes to melt the metal.
No need to add any solder, high efficiency and low cost. Easy to automate and so on. The medium frequency inverter spot welder adopts high-performance pneumatic components. The capstan and the guide shaft are all chrome-plated, and the transmitted pressure is flexible and reliable, and there is no virtual position. The secondary inside of the welding transformer is forced to cool by water, and adopts optimized design, high magnetic permeability material, low no-load loss, strong power output, stability and long life.
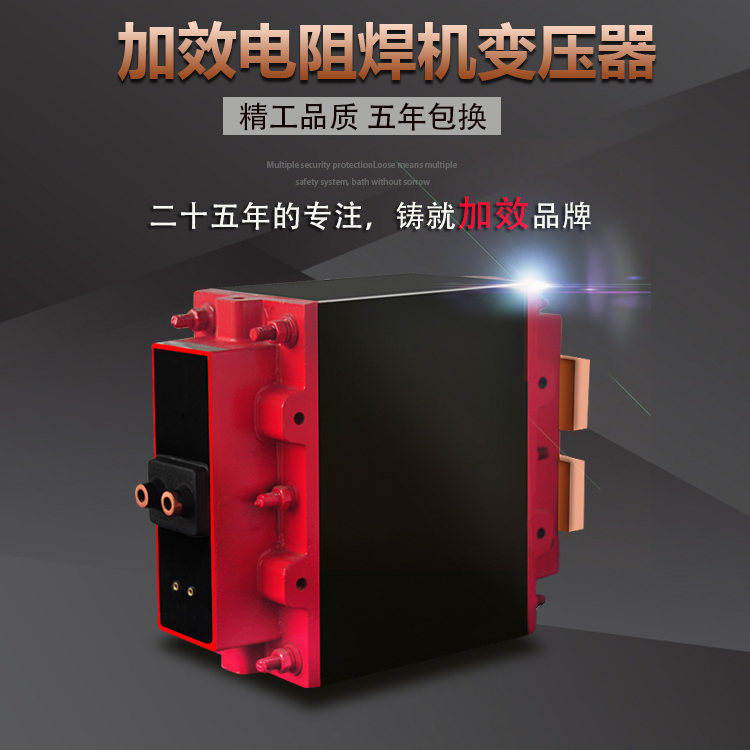
The welding controller is controlled by digital integrated control system or microcomputer resistance controller (optional), with parameters such as pressurization time, welding time, delay, rest, welding current, etc., can be equipped with double pedal, double pulse, double current Control functions, as well as thyristor temperature monitoring. All kinds of welding controllers can meet different functions and can realize multi-purpose of one machine. The welding primary circuit adopts bidirectional water-cooled thyristor control to ensure balanced and reliable current output.